Forging and rolling
ZOLLERN offers forged and rolled products made of copper and copper alloys. The preliminary material needed for forging is produced in-house. The high vertical range of manufacture at ZOLLERN guarantees a high quality and short lead times.
Advantage of forging compared to extrusion
- More uniform structure in forging
- Low risk with respect to internal errors
- Fewer internal stresses
- Low warpage after machining forged material
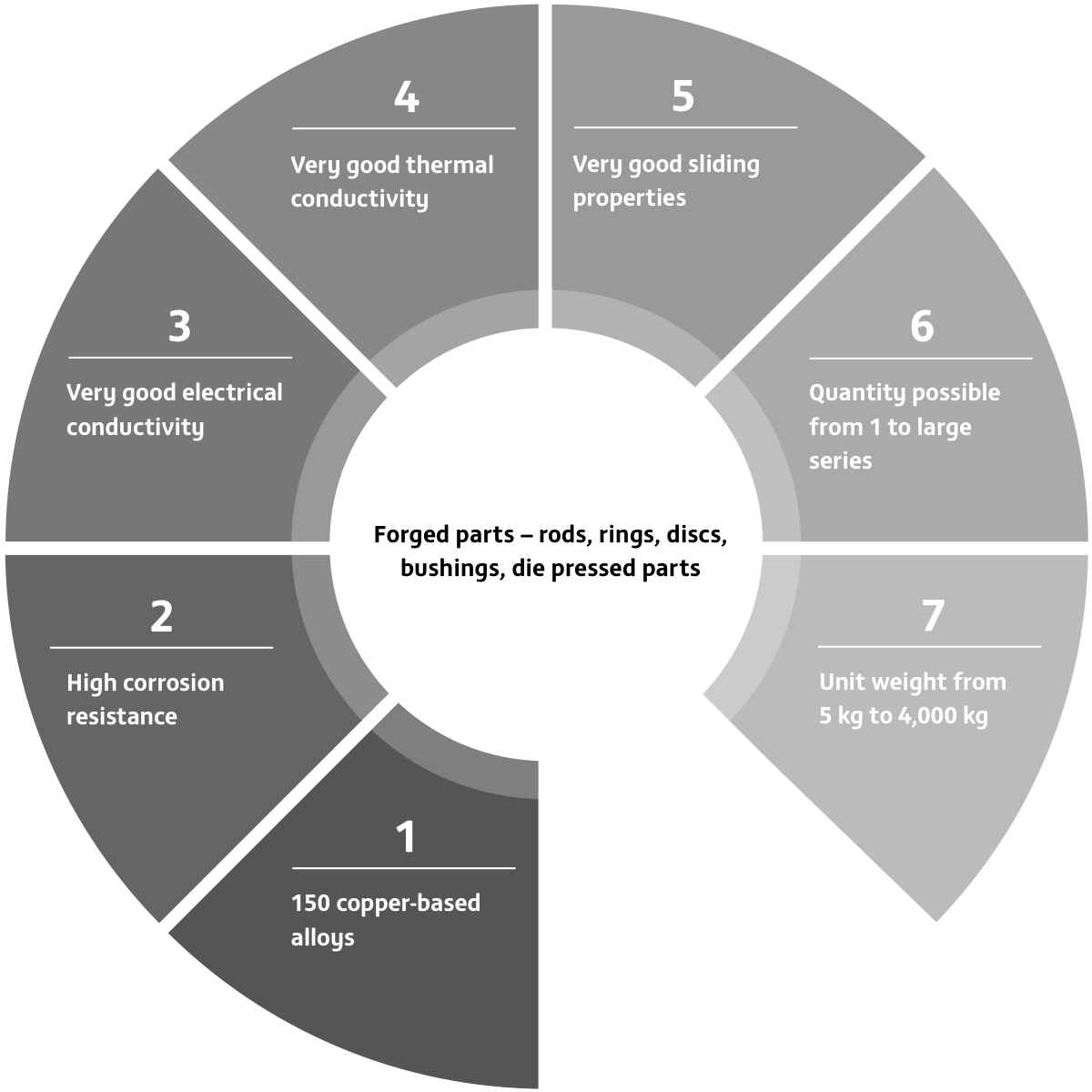
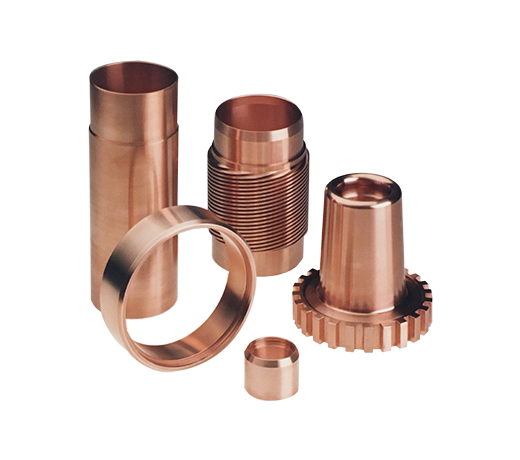
Forgings made of pure copper and copper alloys
ZOLLERN supplies forged products made of pure copper and copper alloys
Unit weight: up to 4,000 kg
Diameter: 28 - 450 mm
Lengths: 10 – 12,000 mm
Forging often transforms the previously coarse-grained cast structure into a fine-grained structure. This increases the strength values, while the toughness and ductility are maintained. Due to the high level of tightness, the forged parts offer a high level of operational reliability under high pressure loads as well as in vacuum applications.
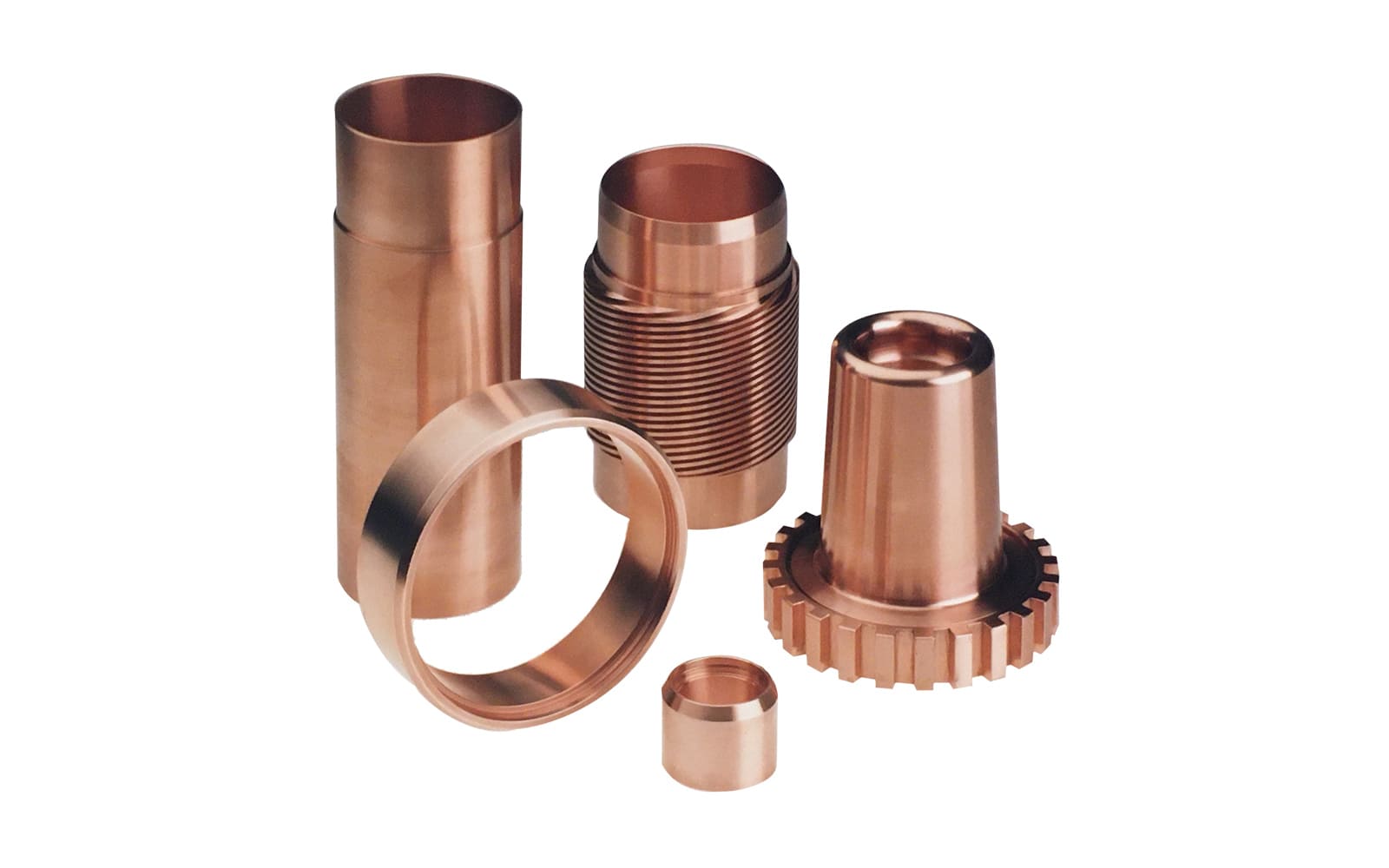
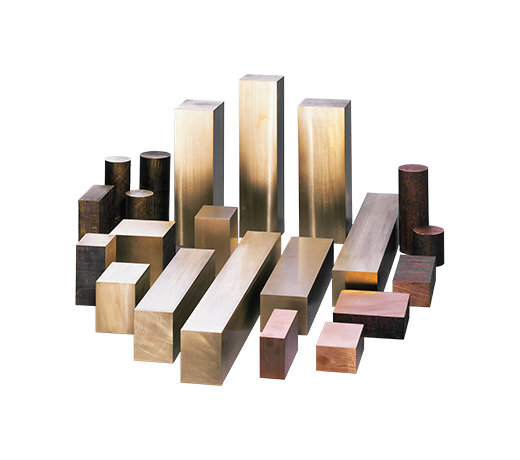
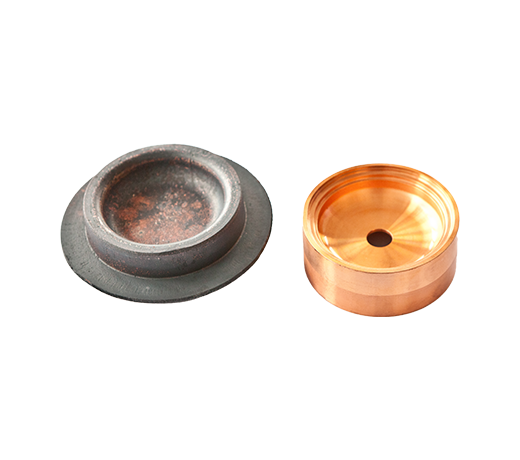
Drop forged parts
Depending on the complexity of the geometry, ZOLLERN produces die-forged parts weighing up to 20 kg.
Due to the near-net-shape moulding, the amount of material used is reduced and the subsequent machining is reduced to a minimum or can be completely done away with.
Drop forging is characterized by a high degree of repeatability and is especially well-suited for large and medium quantities.
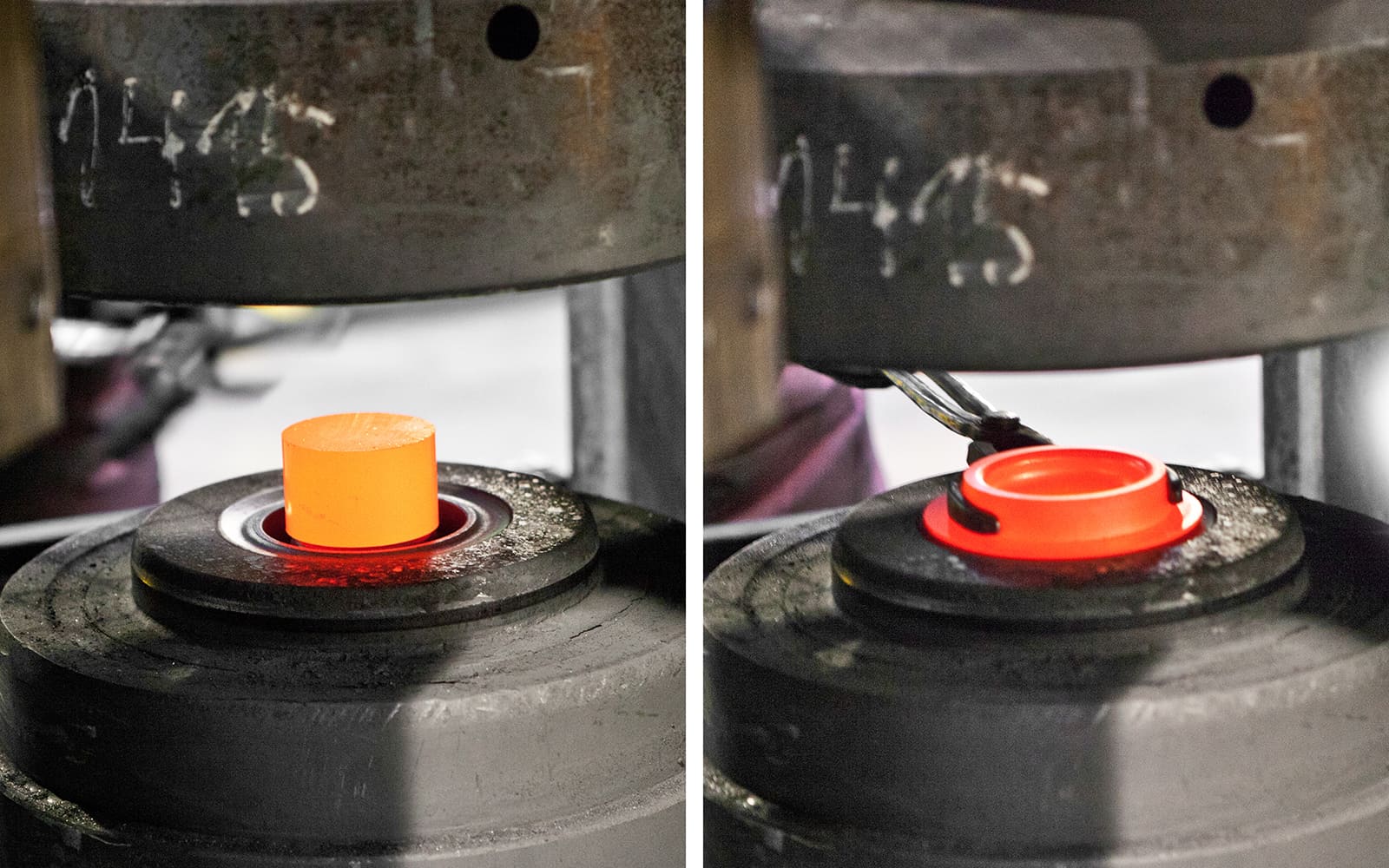
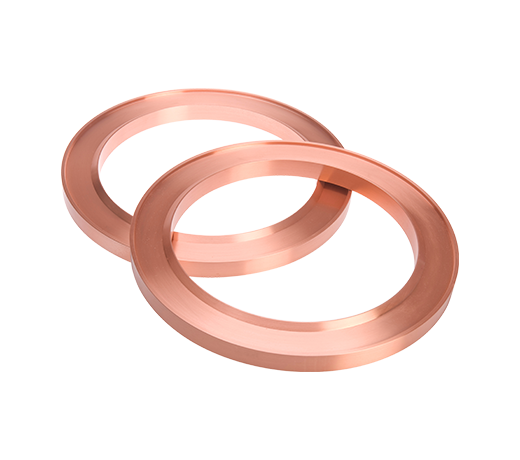
Rings, seamlessly rolled
ZOLLERN offers rings with a unit weight of up to 3.000 kg and an outer diameter of 2,500 millimetres.
Features and advantages:
- Very good kneading
- Near-net-shape surfaces
- Also suitable for smaller quantities
- Short delivery times
- Seamlessly rolled and forged copper rings
- Produced in a modern ring-rolling mill
- First-class surface quality
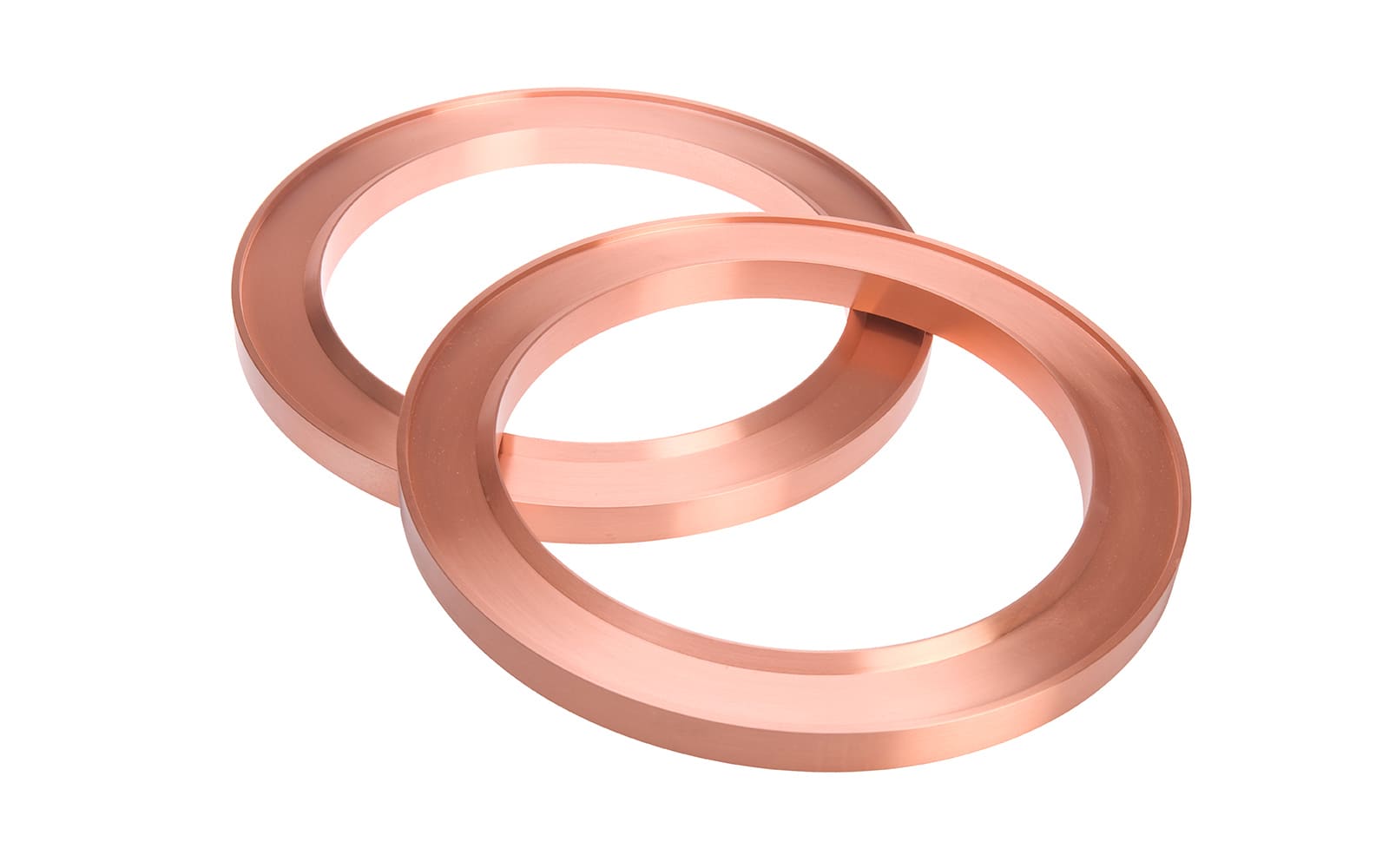
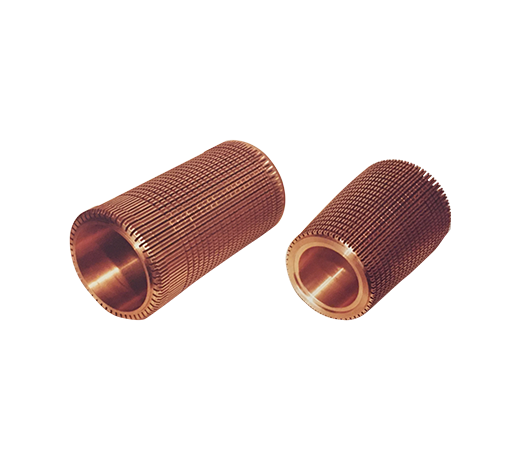
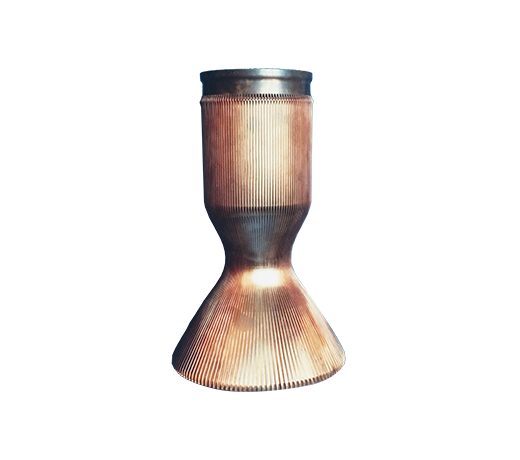
Individual pieces, small series, large series
ZOLLERN produces rings, flat bars and shafts as individual parts, in small series up to large series.
We cover all processes in-house – from melting the alloy, the forming, with or without heat treatment, and a subsequent optional machining and quality assurance.
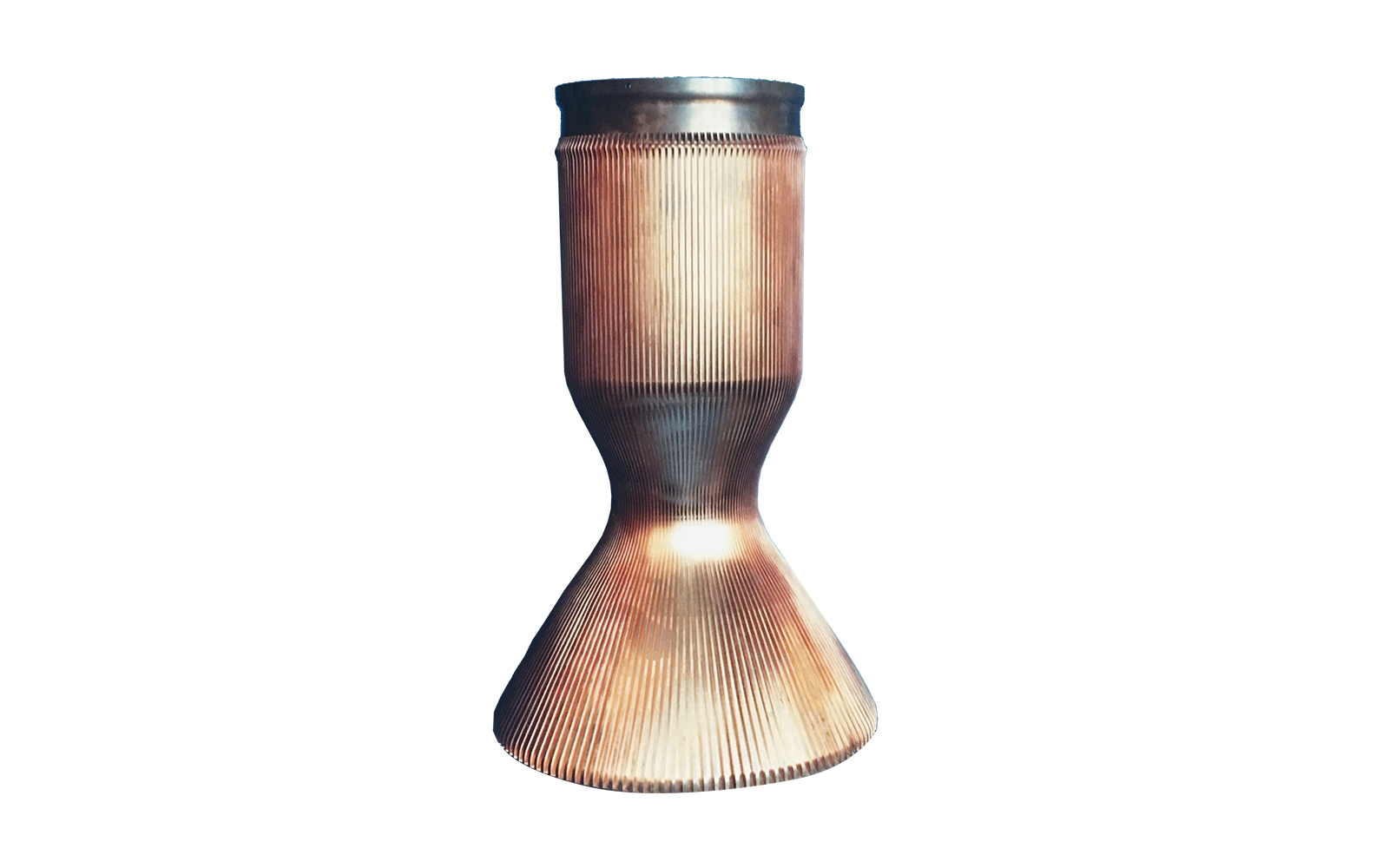
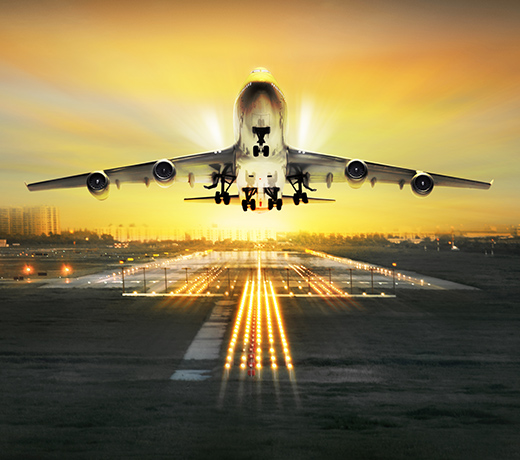
Component solutions for the aerospace industry
ZOLLERN provides advanced component solutions made from copper materials for the aerospace industry. All manufacturing processes are realised in the plant – from melting the raw material and casting through to the finished component ready for installation after non-destructive or destructive testing. Production occurs according to the standards AMS 4881, AMS 4880, AMS 4640, BSB23, UZ19A6.
ZOLLERN semi-finished products for aerospace
- Round bars, forged
- Bars, pressed, drawn
- Bushings, centrifuged, to 500 mm length
Applications
- Landing flaps, landing gear
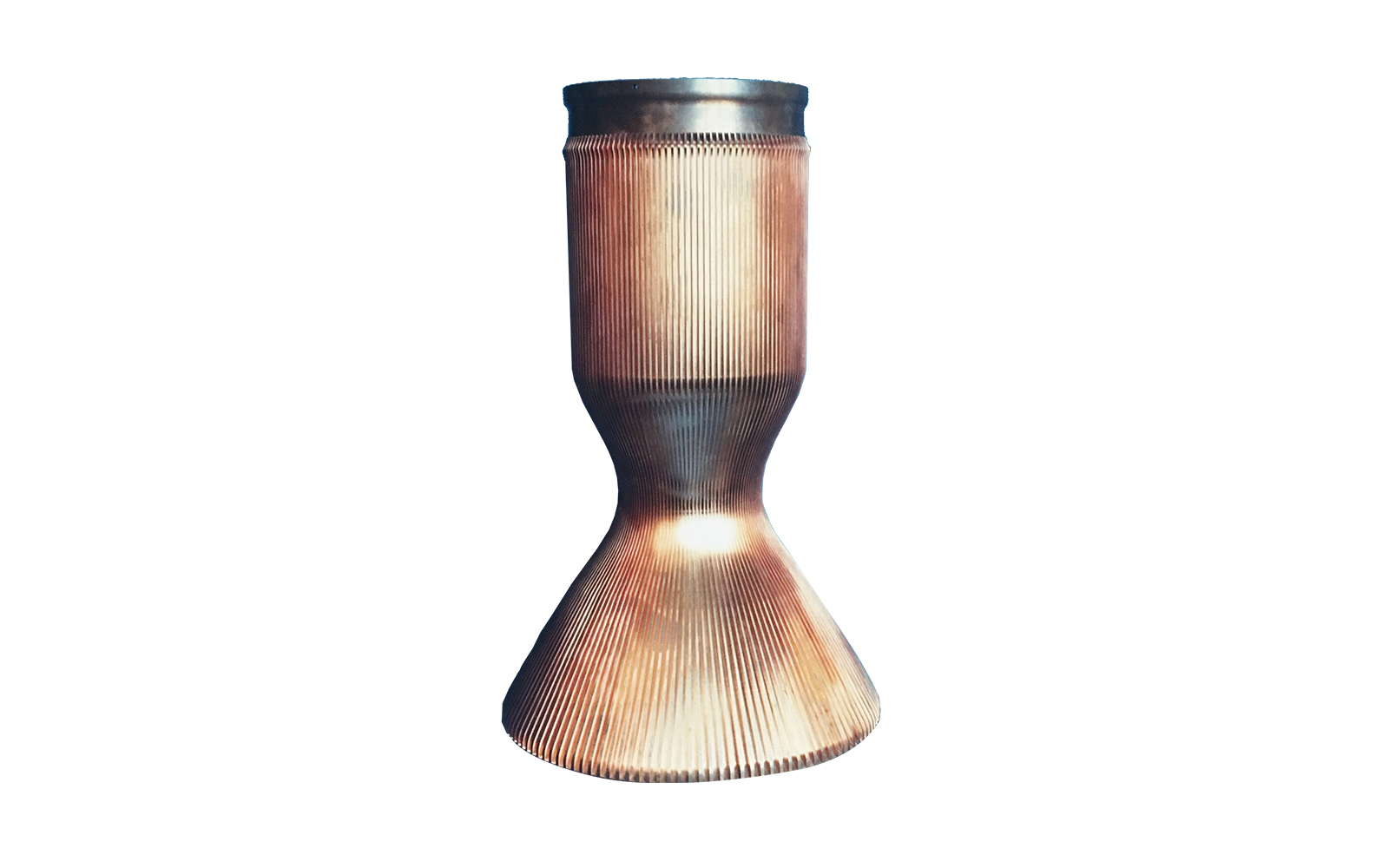
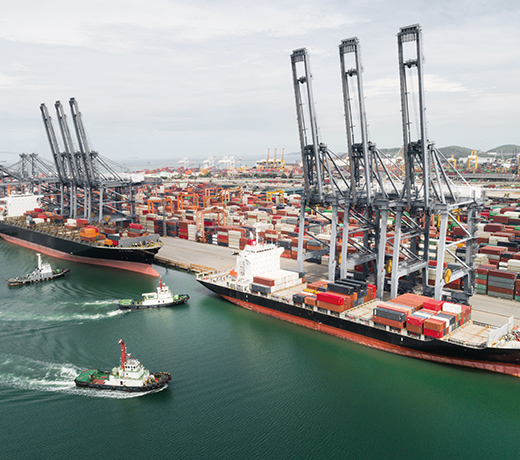
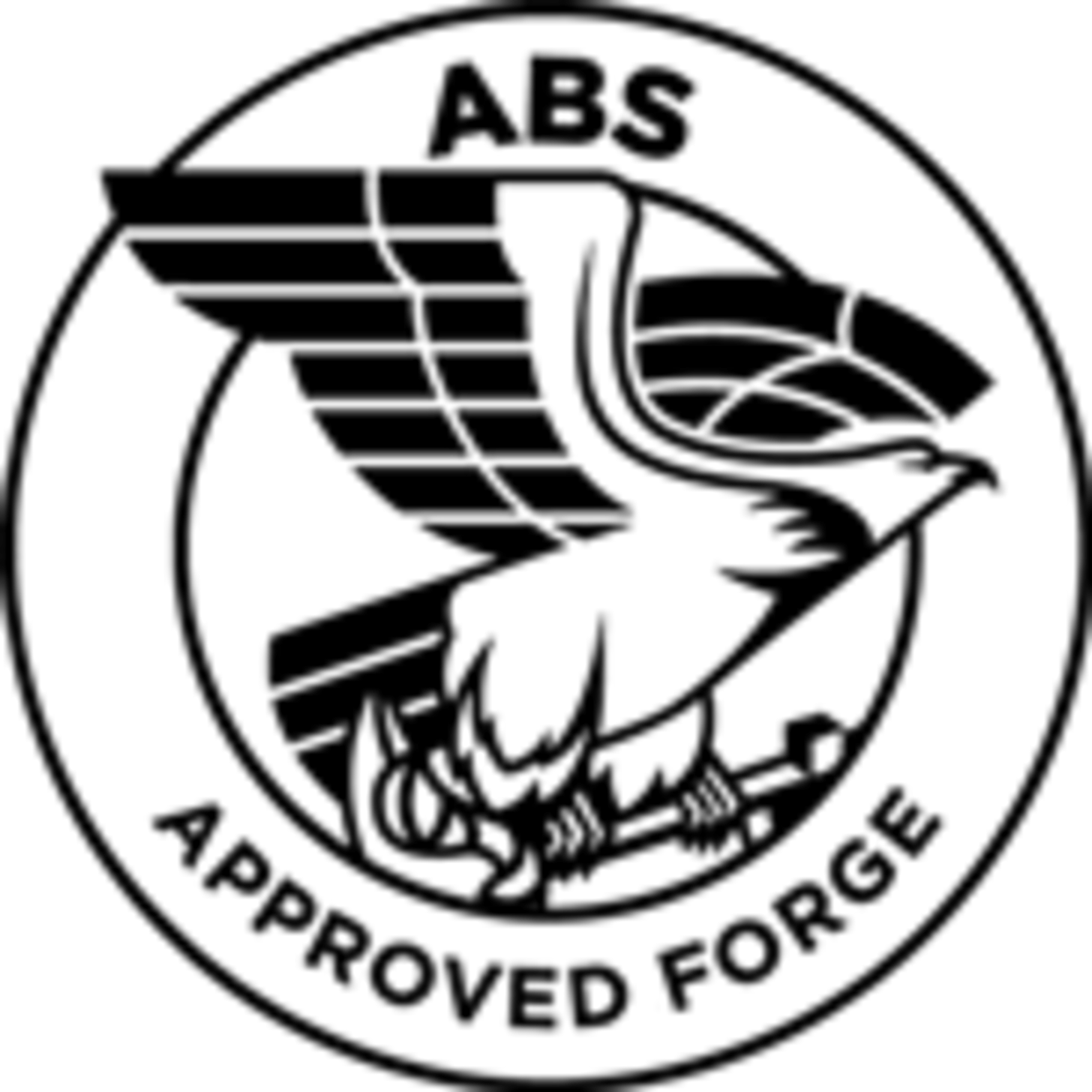
Individual component solutions for maritime applications
ZOLLERN steel alloys and bronze alloys for marine and offshore applications
- Hub housing and propeller blades for marine propulsion systems
- Sliding blocks
- Fittings and valve housing
- Round bars, flat bars, rings
Offshore applications of ZOLLERN forged and cast bronzes
- High-strength and seawater-resistant bushings and washers for jack-up systems on oil production platforms
- Propellers for drives for positioning drilling platforms in deep-sea oil production
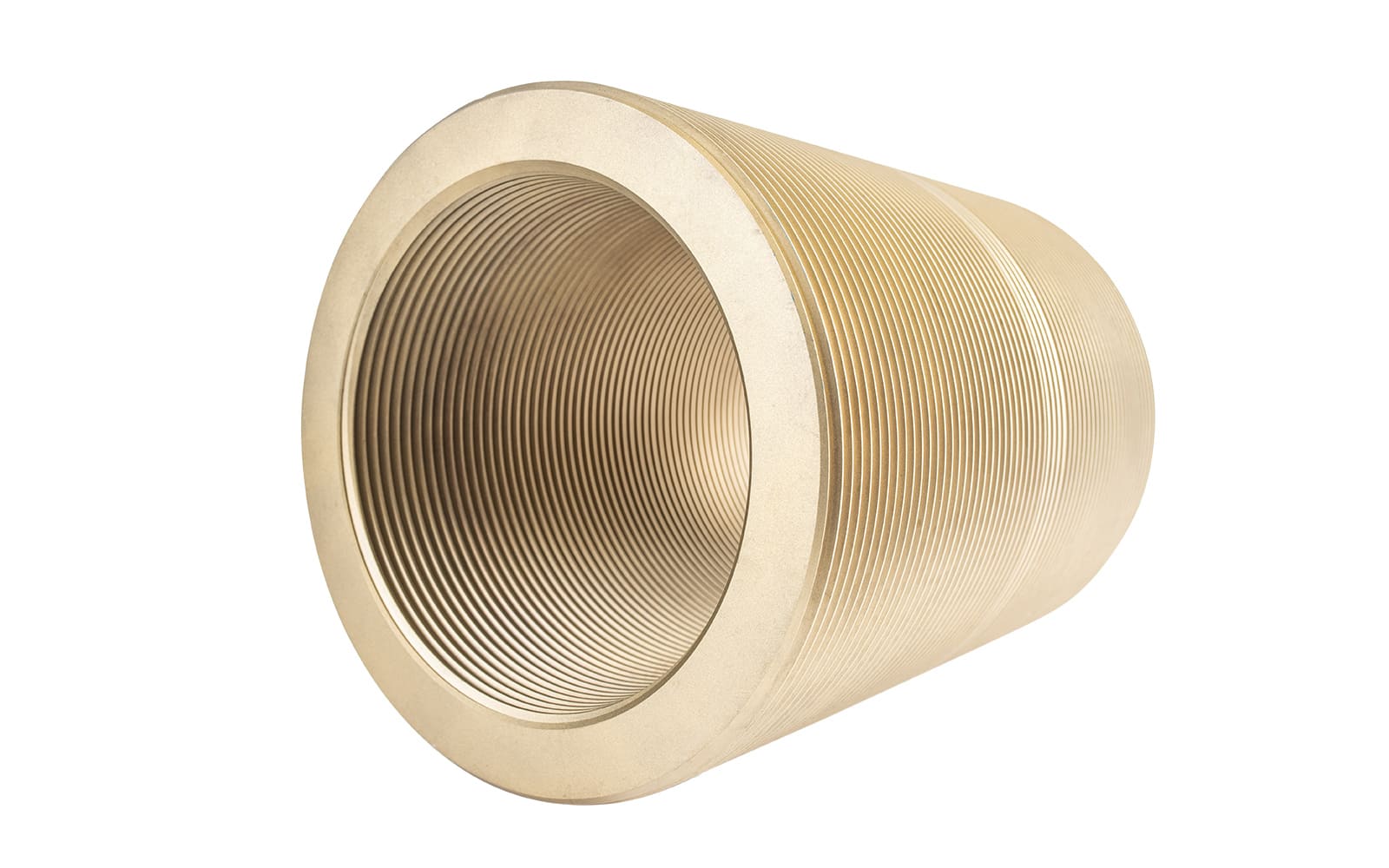
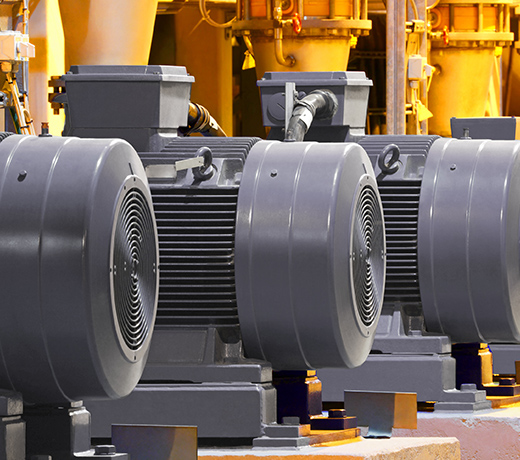
Component solutions for industrial engines and traction motors
- Short-circuit rings, slip rings, short-circuit rods; for larger rotors
- Cap rings made from high-stability copper alloys; for fast-running rotors
- Seamlessly rolled and forged rings in pure copper
- Slip rings
- Rings with external diameters from 200 to 1,600 mm
- Rings in pre-processed and fully finished condition
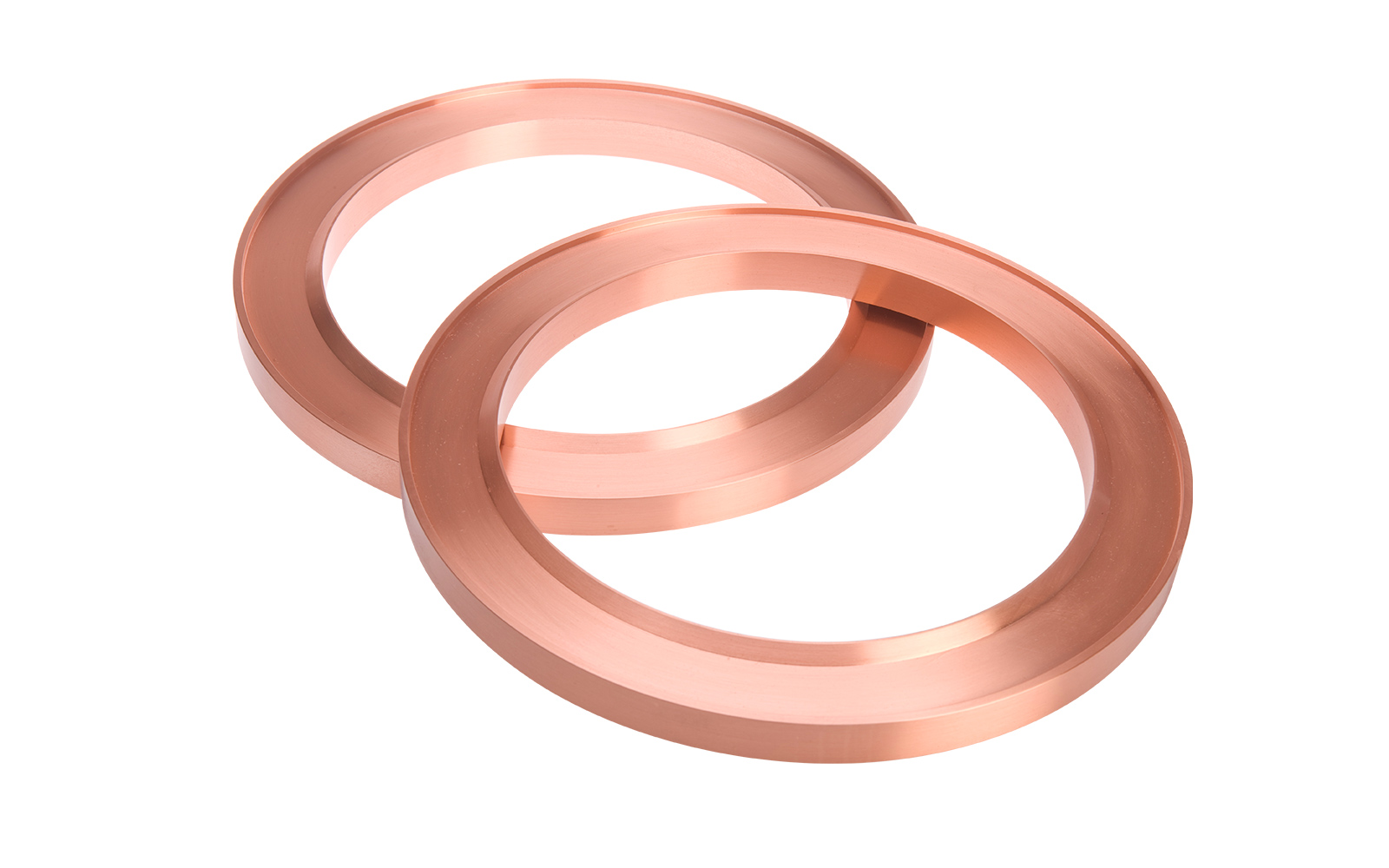
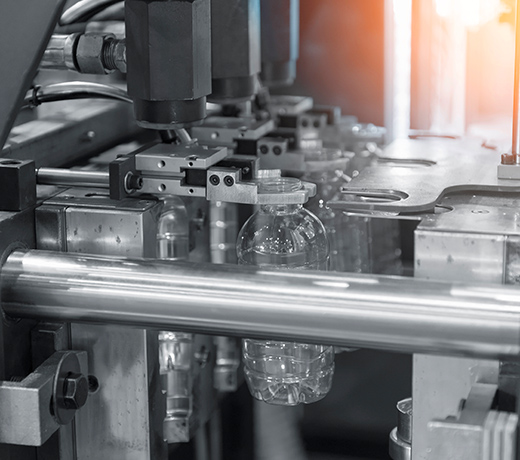
ZOLLERN forged bronzes and complete solutions for general mechanical engineering, forming and mould making
ZOLLERN offers individual component solutions from copper-based materials for machines in sheet metal forming and solid forming.
- Spindle nuts
- Bearing bushes
- Thrust bearing, thrust ring, thrust plate
- Flat guide rails, guide shafts
Custom designs
- High-strength copper-aluminium alloys forged, rolled
- Copper alloys centrifuged or cast in sand
- Mechanically pre-machined or finish machined
- Quality-checked, with factory certificate
- Maximum component quality, very good gliding behaviour, high wear resistance, fatigue endurable
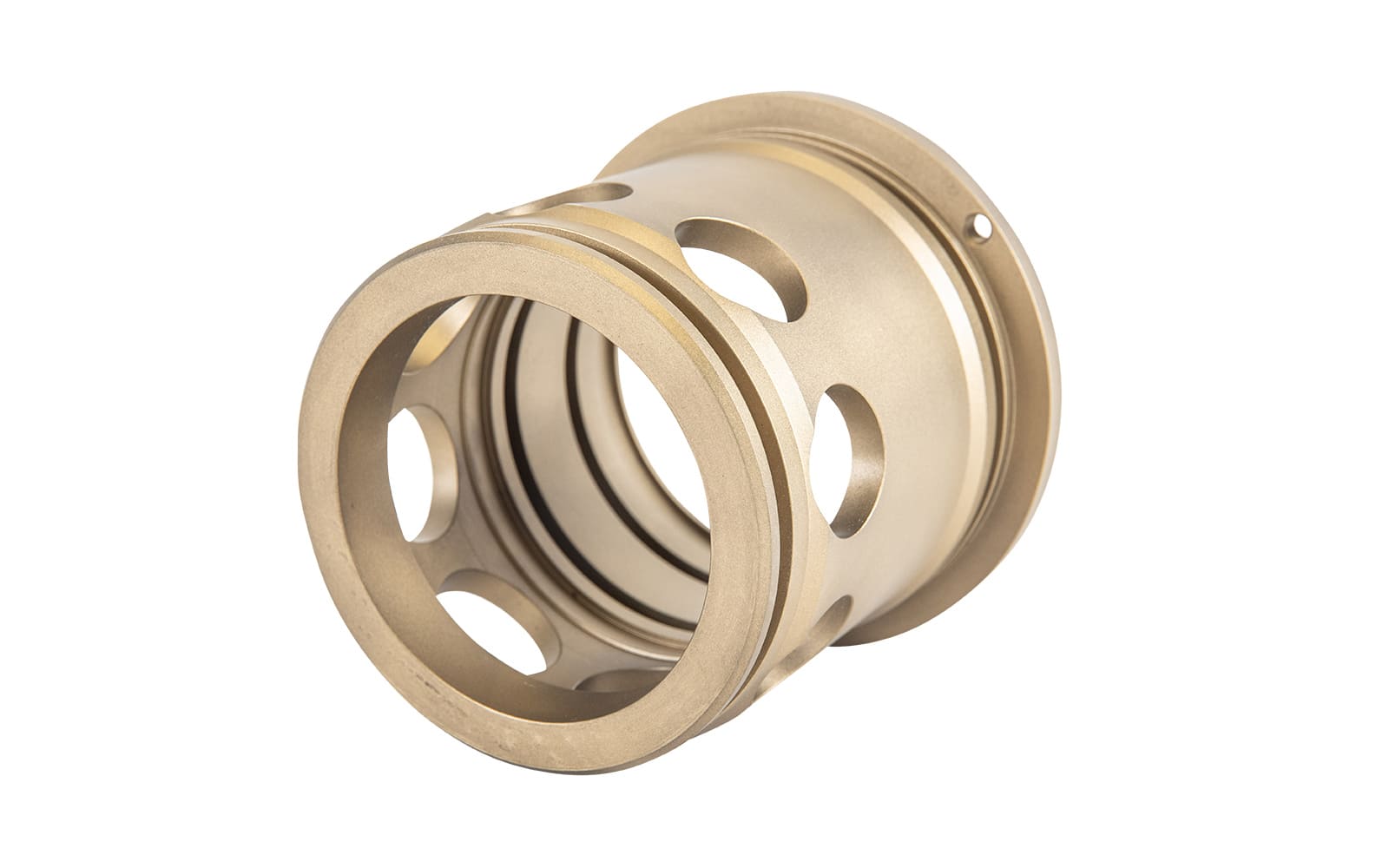
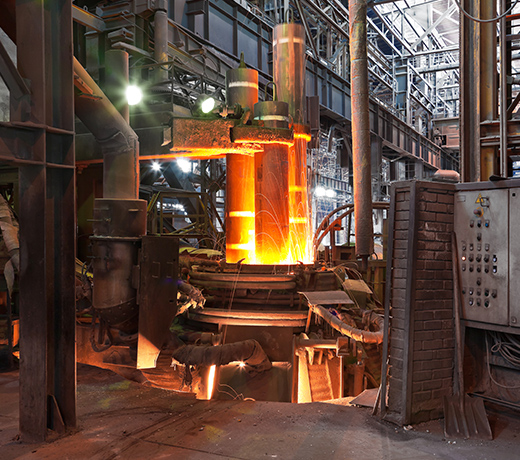
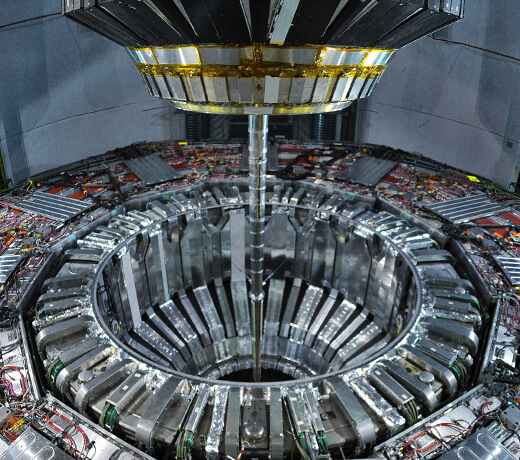
Copper and copper alloys for cooling technology
The high thermal conductivity of pure copper and low-alloyed copper alloys, such as CuCr1Zr and CuNi3Si, is used for heat sinks in different application areas:
- Dies in continuous casting and wire rod plants
- Components for welding systems
- Parts for accelerators in research and medicine
- Rocket nozzles
- Heat exchanger
- Cooling plates, heat sinks in general, also in high-vacuum areas in research facilities
Copper-aluminium alloys, among others, are used for a higher wear resistance, for example in injection tools where the thermal conductivity of steel is insufficient.
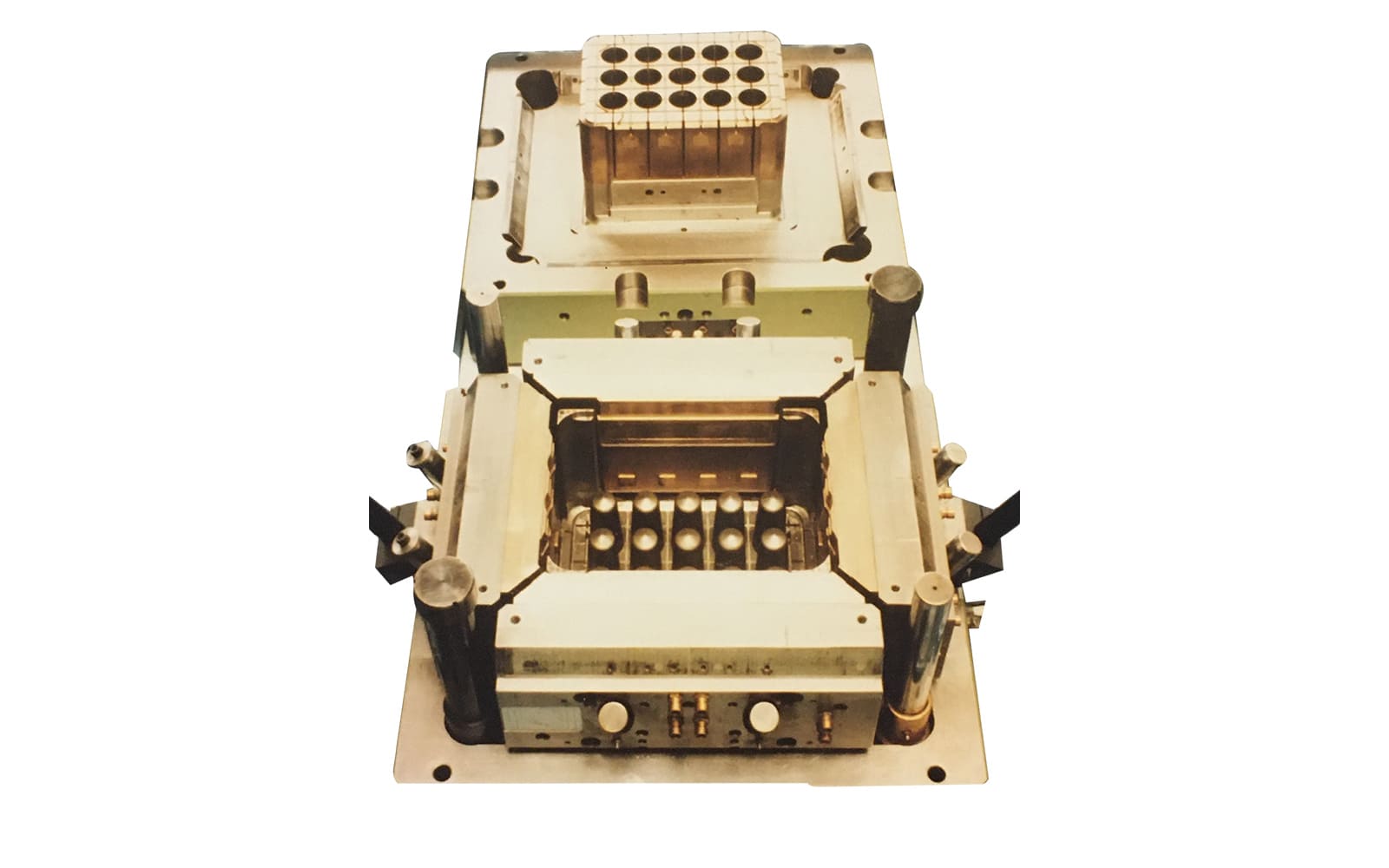
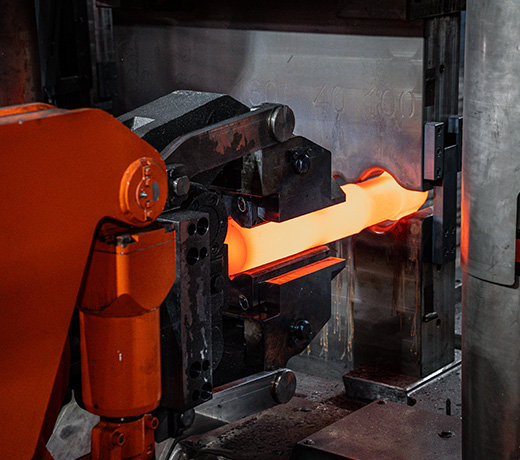
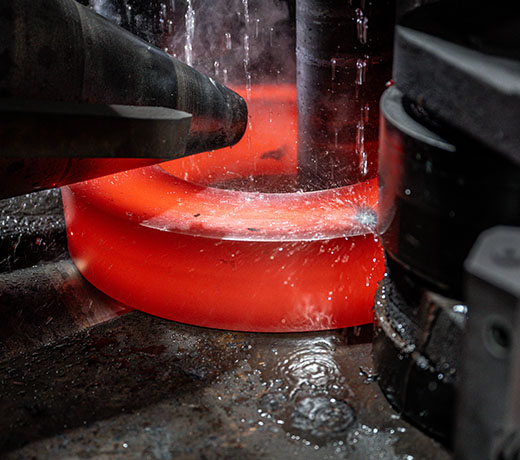
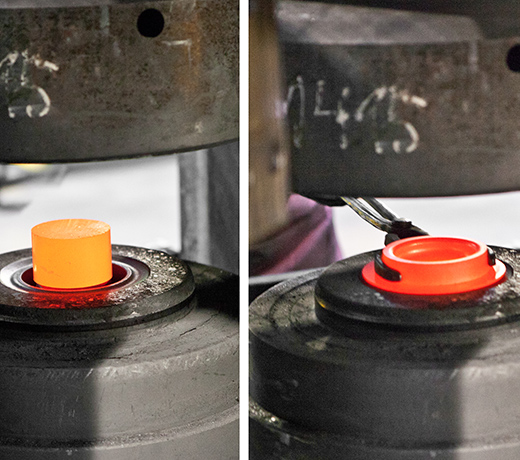
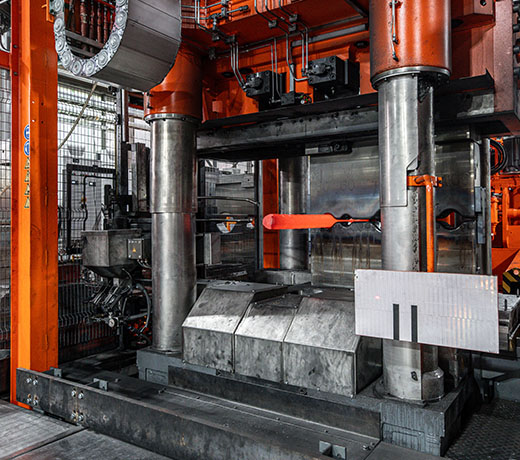
Process chain
ZOLLERN offers a high vertical range of manufacture for efficient processes and first-class quality.
- Master forming
- Metal forming
- Separating
- Changing material properties
- Machining
- Heat treatment
- NDT tests according to customer requirements (PT/UT/MT)
- Material testing (tensile test, notched bar impact test, hardness test, electrical conductivity)
- Metallographic examination (grain size determination, microstructure assessment, etc.)
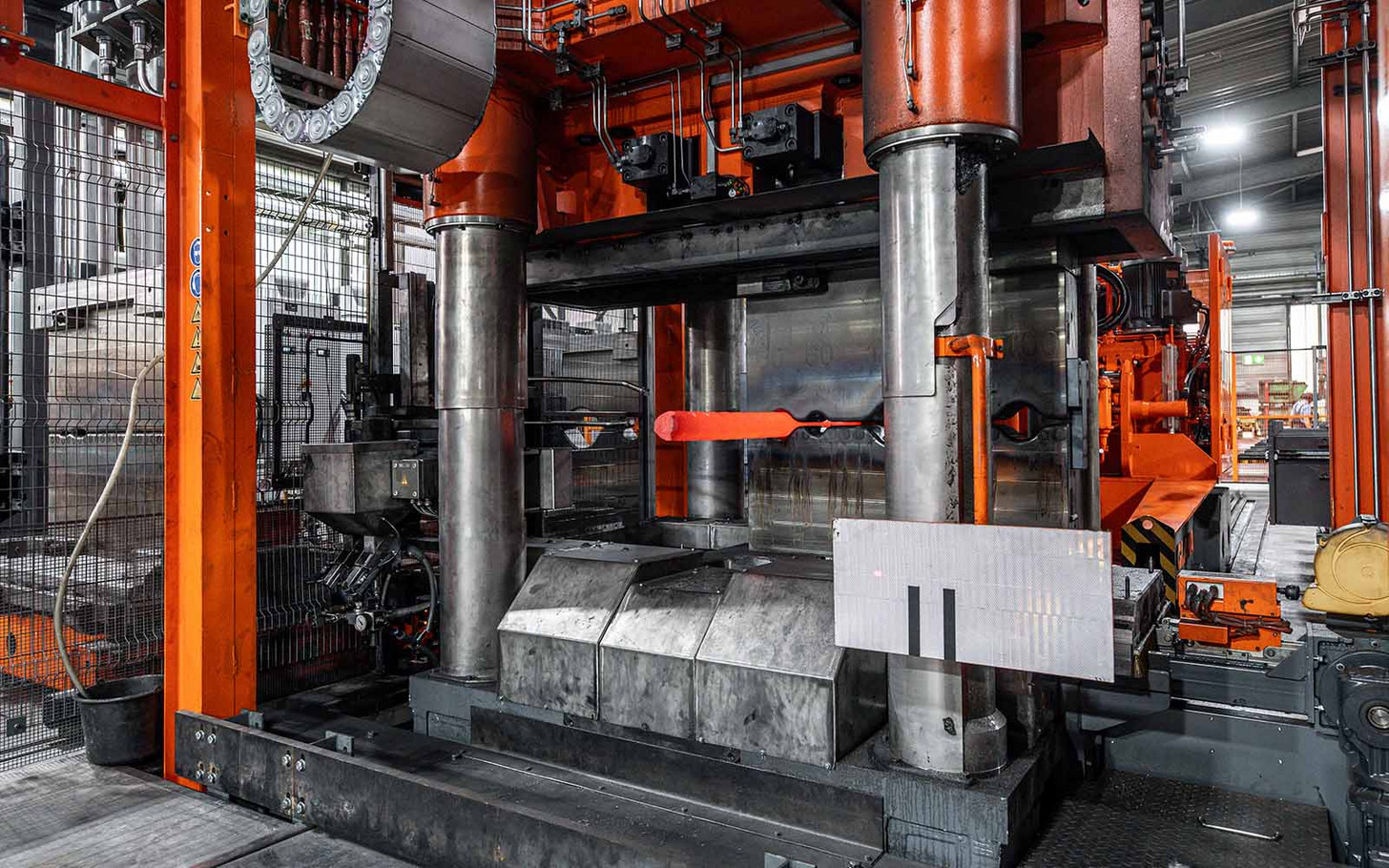
Alloys, standards, specifications
ZOLLERN supplies forged parts, rolled components and rings made of copper and copper alloys according to national and international standards, as well as according to customer-specific standards:
- DIN
- EN
- ASME
- ASTM
- AMS
- AD2000
- NSMT
- French or British standards
- Customer-specific requirements with increased strength values or other quality characteristics are possible by request
- Def Stan
- MIL
Alloy groups
- Copper-aluminium
- Copper-zinc
- Copper-chrome-zirconium
- Copper-nickel
- Copper-nickel-silicon
- Pure copper
- Special alloys with a copper basis