Individual component solutions
ZOLLERN offers individual component solutions and customer-specific castings from large series to individual pieces. We are development partners for our customers and one of the leading foundries in Europe with more than 1,000 employees in the casting business area.
Casting is a precision process. It offers tremendous freedom of design. The wide range of possible alloys makes economic solutions possible for the most varied of applications.
- Over 500 alloys in-house
- Unlimited design freedom, near net shape
- Accurate machining tolerances allowance 0,3 - 1,5 mm
- Economic solutions
- The highest quality level
- Materials development
- Concurrent engineering
- Customer service worldwide
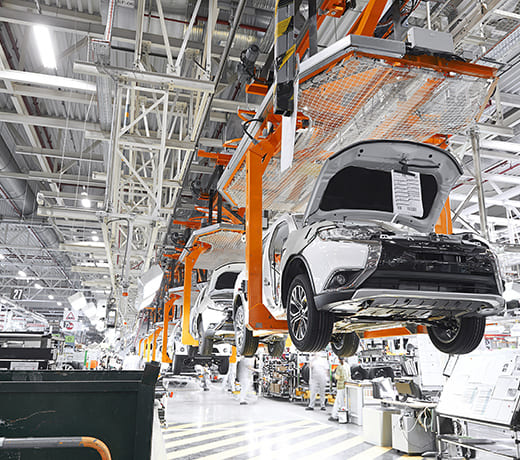
Automotive
Investment cast components are established in the automotive industry due to their enormous performance capability. ZOLLERN meets the demand for efficiency and performance with its high-quality components, such as turbine wheels for turbochargers. In the investment casting process, highly complex geometries can be reproduced in the most resistant materials with the highest process reliability.
- Turbine wheels
- Flap plates and bushings
- VTG vanes - guide vanes
- Finger followers
- Planet carriers
- Wheel carriers
- Brakets Formula 1
- Housing
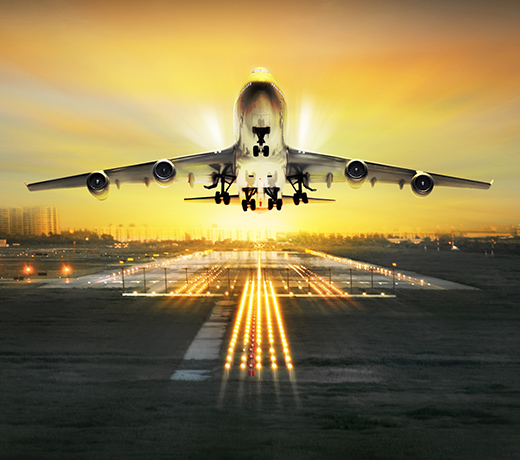
Aerospace
Eco-efficiency and alternative drive concepts with reduced fuel, noise and emissions are key objectives in the aerospace industry. Lightweight designs and simultaneously highly durable investment casting solutions from ZOLLERN help to achieve these objectives in many different alloys. The stringent quality assurance and a certified management system confirm the high quality of our services and products:
- Guide and rotating blades, vanes, heat shields
- Landing flap profiles, landing flap receptacles, housing
- Landing gear and structural castings
- Housing for optical, electronic and fuel systems
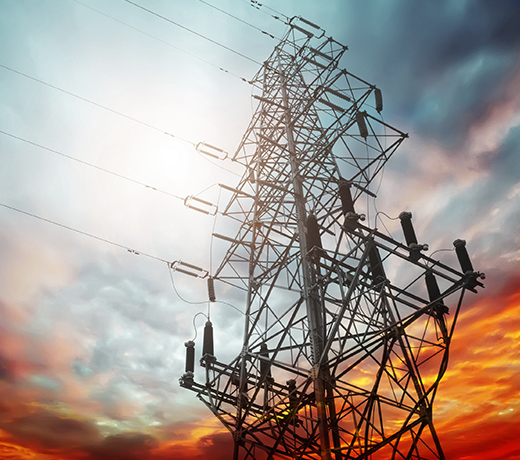
Energy
High-performance castings from ZOLLERN are important components in plants that generate energy. These are often key components in different industries
- Oil & Gas Industry
- Water
- Coal
- Renewables
- Nuclear
For example they are used as:
- Structural components, vanes and blades for gas turbines
- Core Parts for Drilling Devices
- Kaplan blades, guide vanes
- Stator press rings for generators
- Blades for REA fans
- Pole heads and pole carriers
- Burner components for gas turbines
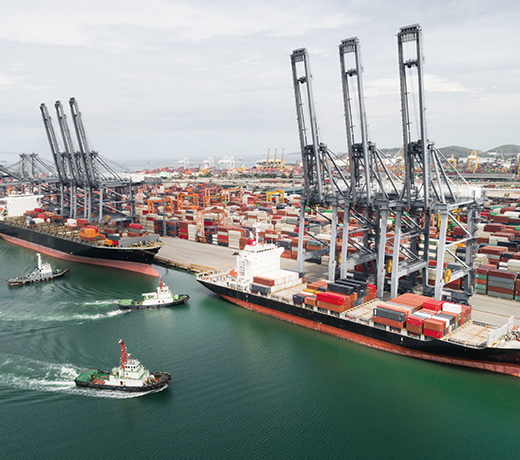
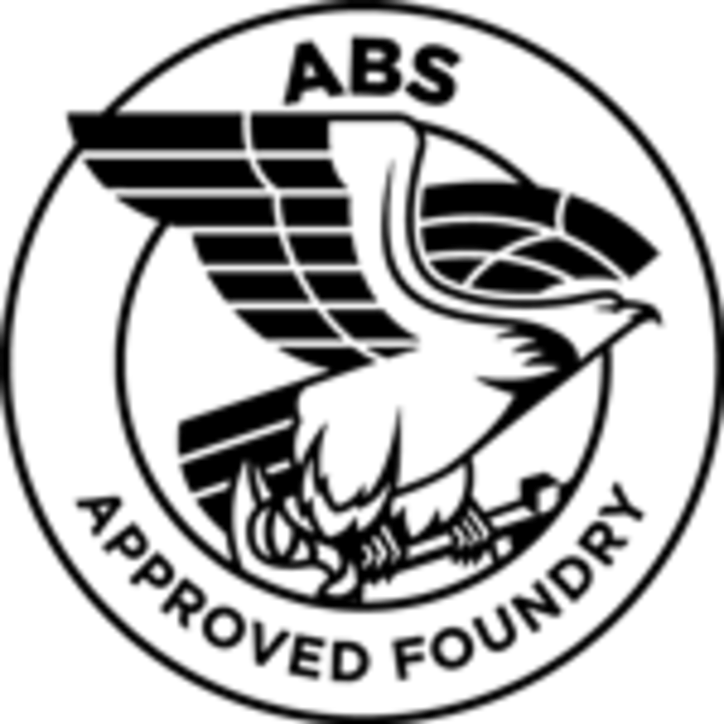
Maritime
Cast components made of copper alloys and steel alloys impress in maritime application due to their corrosion resistance, geometric complexity and particularly high casting quality:
- Fixed propellers as well as hub housings and blades for variable pitch propellers
- High-pressure fittings and safety fittings for submarines
- Valve housing for exhaust gas routeing, seawater treatment and ballast water treatment
- Engine housing
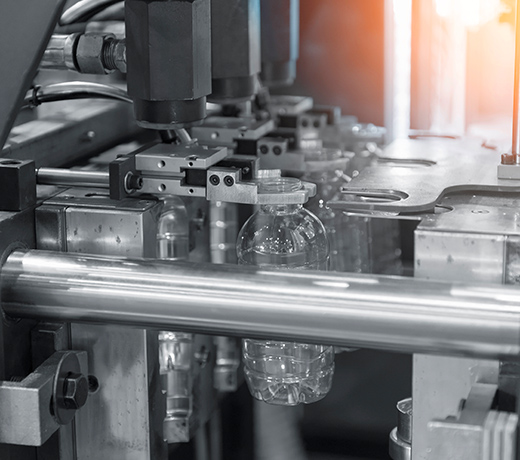
Industrial Components
The sophisticated casting solutions of ZOLLERN meet the highest requirements in almost any technical sector. For example ZOLLERN supplies:
- Castings for mechanical engineering
- Rings and segments for slewing bearings
- Dies for quartz glass production
- Housing and cover, for example for heat exchanger
- Castings for food and packaging machines
- Electrode holder with cast-in cooling tube
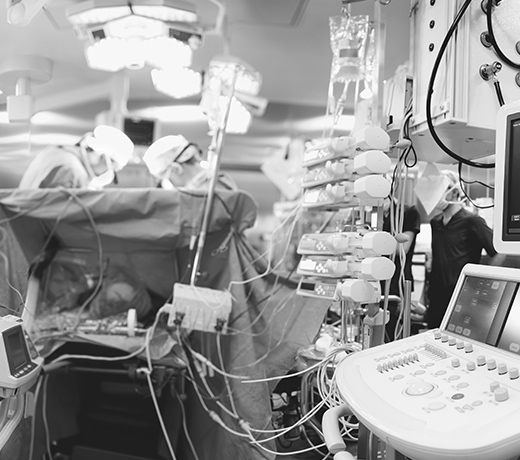
Medical
We produce highly complex components for medical technology in a large number of materials. The application areas are:
- Implants (e.g. hip and knee)
- Surgical equipment
- Medical instruments and accessories
- Laboratory technology
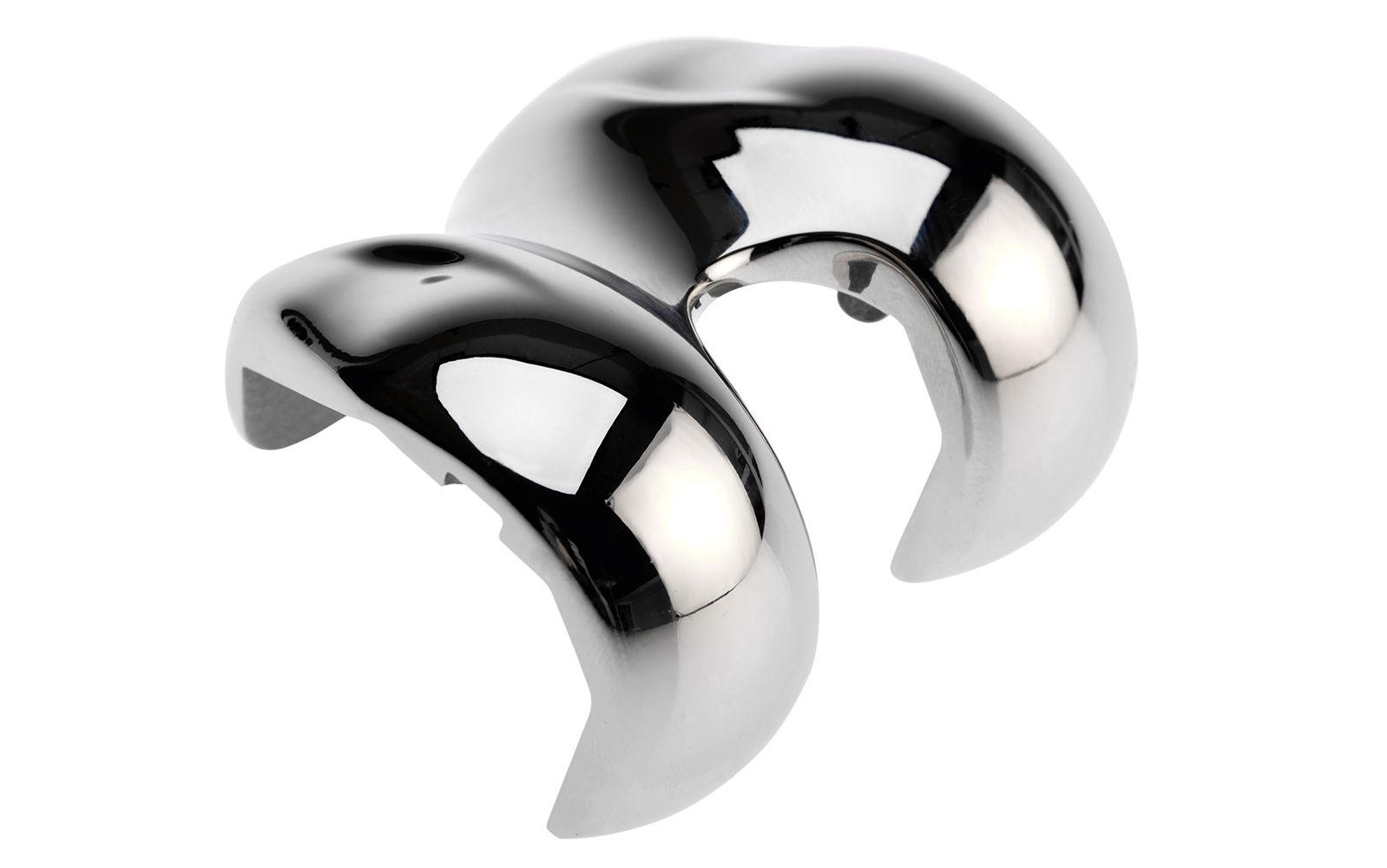
Description: Implants in superalloys, knee- and hip
Application: Medical
Alloy: Cobalt-Alloy
Manufacturing Process: Roll-Over
Customer: International medical companies
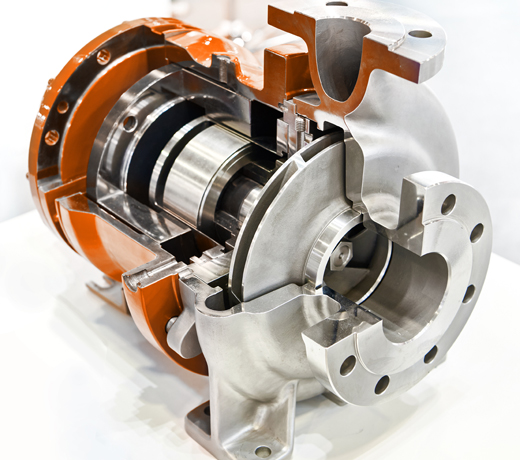
Pumps
Cast parts made of copper and nickel-based alloys, high-alloy steel grades, duplex, super duplex withstand high pressures high pressures and are resistant to corrosion and abrasion. They are used in pumps on land as well as above and under water.
- Piston pump housing
- Spiral housing
- Impellers
- Impeller hubs
- Blades
- Wear rings
- In feed pumps for oil & gas, medical technology, food, fresh water and waste water.
- In coolant pumps for nuclear power stations as well as surface and underwater vessels.
- In extinguishing pumps, in pumps on submarines and drilling platforms and other maritime applications.
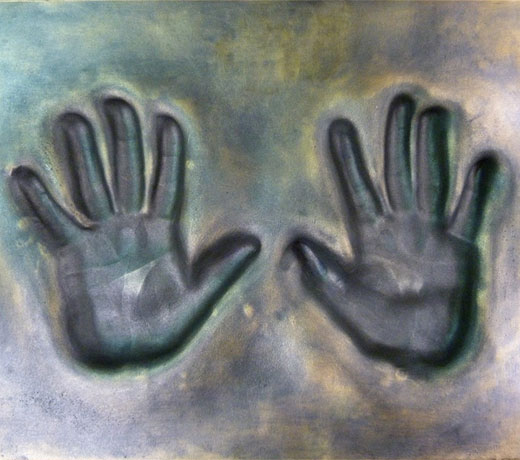
Arts
We transform artists’ ideas into unique cast products using CAD and cast simulation applications and plenty of experience in art casting. Castings are made for sculptures, for example, that meet very specific quality requirements.
Controlled solidification during the casting process creates almost pore-free surfaces under the casting skin. The model-free production using moulding material milling increases the economic efficiency of the artistic cast products.
- Arts and art castings, manufactured according to data set and milled mould or according to any model, built from segments or cast as a monoblock.
More than 500 alloys for individual requirements
ZOLLERN casts almost every standardised alloy. Even non-standardised special alloys are created according to customer requirements or modified using existing alloys.
Investment casting alloy groups
- Iron and steel alloys
- High-temperature and heat-resistant steel casting
- Tool steels
- Case-hardening steels
- Quenched and tempered steels
- Rust and acid-resistant steels
- Special materials
- Nickel-based superalloys
- Non-directional solidified (EQX)
- Directional columnar crystalline solidified (DS)
- Monocrystalline solidified (SX)
- Cobalt superalloys
- Stellite
- Implant materials
- Aluminium alloys
Steel and bronze alloys (sand casting and other casting processes)
Steel alloys (sand casting and other casting processes)
- High alloyed
- Special materials available by request
- (Nickel basis, copper basis, Hastelloy)
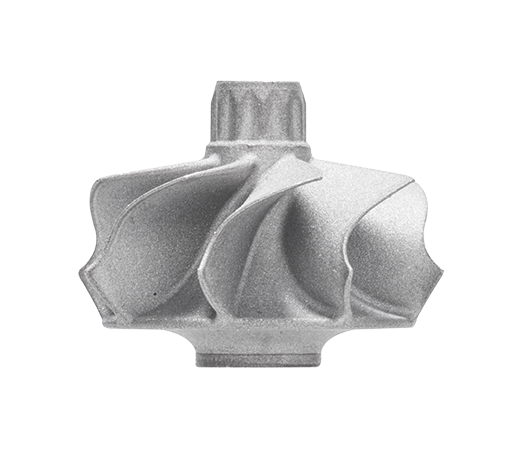
Vacuum investment casting
Ground tapping method
Highly productive melting and casting process for complex components made of highly heat-resistant materials. Large quantities can also be produced in a short period of time with a very high level of reproducibility.
- From individual parts to large series
- High degree of purity
- Possibility of targeted grain refinement on the castings
- High degree of automation
Tilting crucible method
Melting and casting process for the production of complex components made of high-temperature resistant materials with a high purity and very good reproducibility.
- From individual parts to large series
- Very high degree of purity
- High degree of automation in production, autonomous casting by casting cell (pre-heating to cooling)
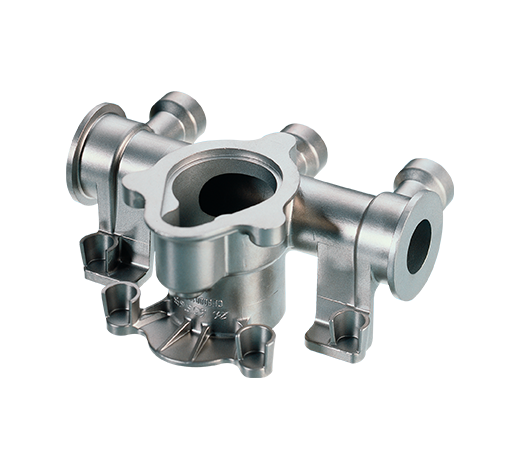
Open air investment casting
Conventional method
The conventional open investment casting - is a lost wax process that is characterised by an almost unlimited selection of alloys.
- Component weight up to 100 kg
- Manual pouring off of the casting cluster in an oxygenated environment
- The mould is filled manually via a ladle and is controlled by the casting speed
- Maximum installation space 600 x 600 x 550 mm
Roll-over technology
A very high material quality is achieved with roll-over technology. After melting the alloy, the furnace rotates 180 degrees in a few seconds. The mould shell that is flanged directly to the furnace is filled precisely and with low turbulence in the process, also while using inert gas.
- The influence of oxygen is eliminated by using an inert gas bell.
- The maximum installation space is 580 x 400 mm diameter
- Maximum casting weight of 100 kg
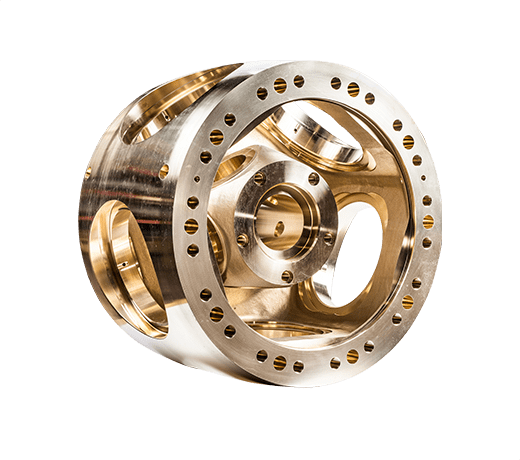
Sand casting
The sand casting process offers a high degree of freedom and the economic production of complex components with undercuts and cavities
- For individual parts and small series
- Production according to the permanent model, lost model or based on printed/milled moulded parts
- Part weights: Copper alloys up to 8,000 kg, steel alloys up to 2,500 kg
- Production using a lost mould
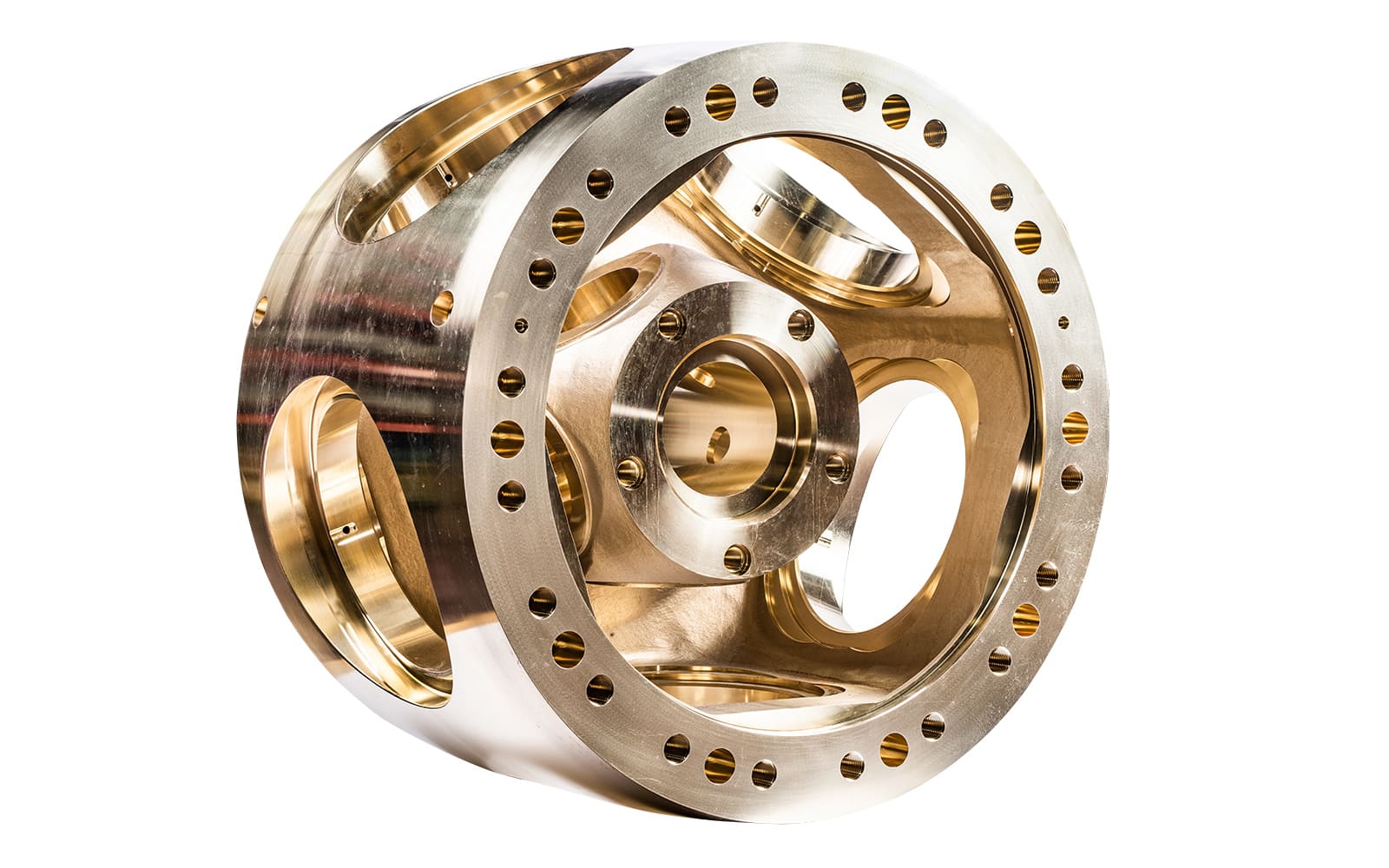
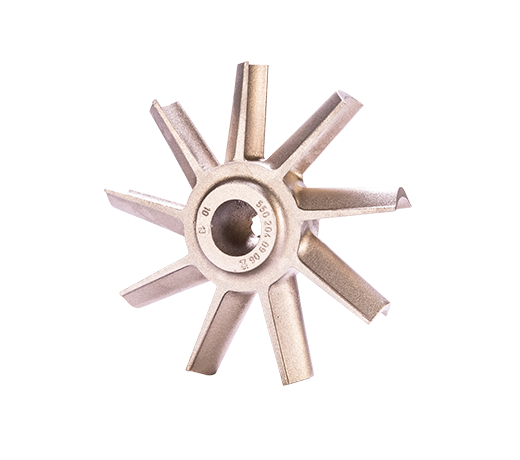
Croning casting / shell casting
Complex components with cavities and a high surface quality can be economically produced with Croning casting or shell casting.
- Surface quality Ra 6.3 µm
- Large series
- Metallic models
- Weight range up to about 20 kg
- Part dimensions up to about 400 x 250 x 200 mm
- Production using a lost mould
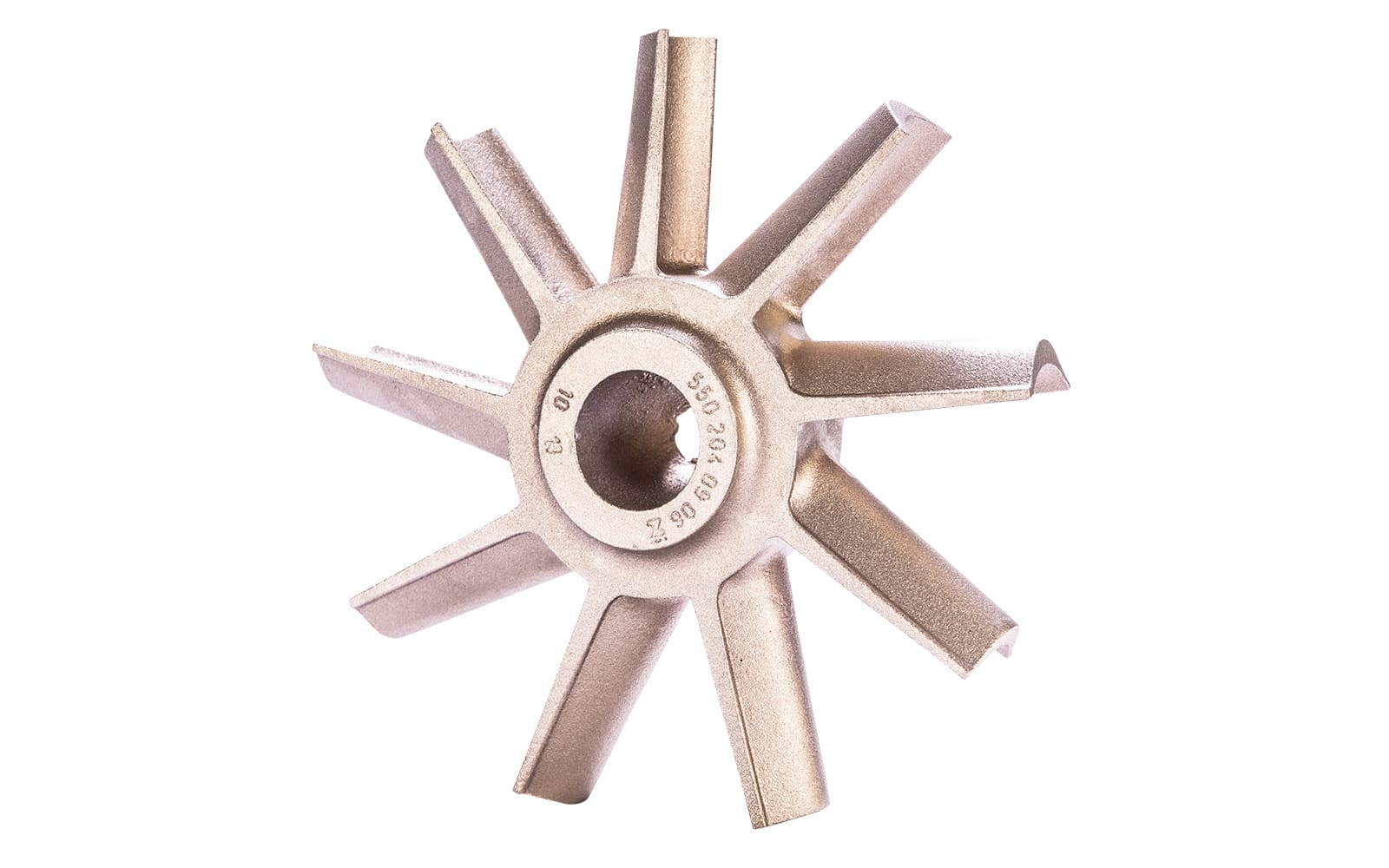
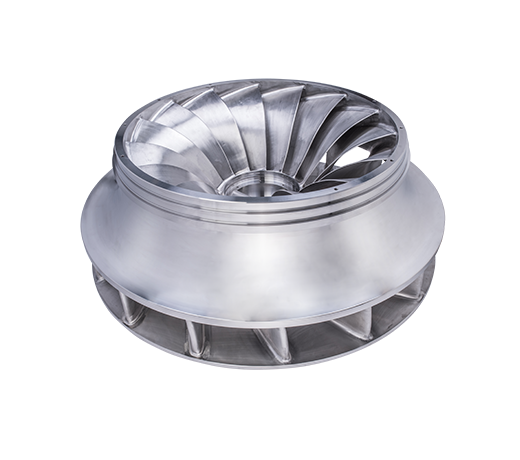
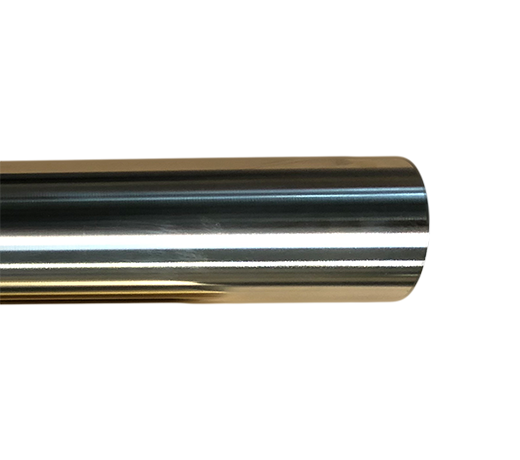
- Development partnership - from the idea to the finished product
- Casting optimisation and simulation
- Model-free production
- Technical consultation
- In-house Toolmaking
- Investment Casting
- Investment casting Alloys
- Sandcasting, Alloys
- Cast Steel and Copper Casting Alloys
- Sandcasting for aviation
- Sandcasting for maritime and offshore
- Sandcasting for forming, molding
- Sandcasting hydroelectric turbines
- Investment casting for automotive industry
- Castings for gasturbines, aero-derivates
- EN 9100 Portugal
- EN 9100 Ravne
- EN 9100 ZGF ZGM Laucherthal Portugal Ravne
- IATF 16949 Portugal
- IATF 16949 ZGF ZST Laucherthal
- ISO 9001 ZGF ZST Laucherthal
- ISO 9001 Romania
- NADCAP NDT ZGF Laucherthal
- NADCAP Welding ZGF Laucherthal
- ISO 14001 Environmental Management System
- ISO 50001 Energy Management System
- ABS ZGM Foundry Laucherthal